Session Aims & Scope
Digital twin (DT) has been a prevailing topic in both academics and industry, owing to the rapid development of artificial intelligence, cyber-physical systems, and digital technologies. The core idea of the DT is to develop a virtual replica corresponding to the physical entity. Through the real-time interaction between the virtual and real spaces, the system can display and analyze the state of the physical entity, and make further decisions on it. As an enabling technology of intelligent manufacturing, the DT has been used by many scholars to build the manufacturing system, that is, the DT-driven manufacturing system (DTMS). Previous research has demonstrated that DT has great potential in manufacturing. Therefore, in order to make the latest research present at the DigiTwin 2023, the conference is extending a call for papers, and a special session on Digital Twin-driven Manufacturing System is focused.
The session will focus on the following points
- Digital twin-driven process planning stage
- Digital twin-driven decision-making in the manufacturing process
- Digital twin-driven self-organization between multiple manufacturing systems
- Digital twin-driven self-adaption for dynamically changing requirements
- Digital twin-driven collaboration among multiple manufacturing systems
- Digital twin-driven autonomous interaction during the manufacturing process
- etc.
Session Chair(s)
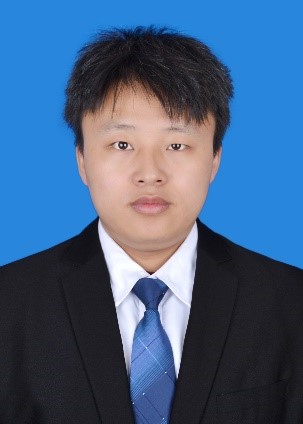
Chair
Shimin Liu
Postdoctoral fellow ,Hong Kong Polytechnic University
shimin.liu@polyu.edu.hk
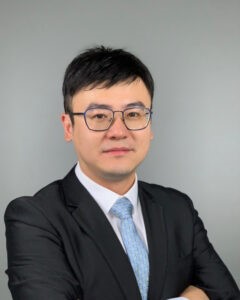
Co-Chair
Zheng Pai
Associate Professor , Hong Kong Polytechnic University
pai.zheng@polyu.edu.hk
Session Presentation
1.
Zhiwen Lin
School of Mechanical and Aerospace Engineering, Jilin University
Title:Research and Application of Digital Twin Systems for Discrete Manufacturing
Abstract
The digital twin workshop within the discrete manufacturing exemplifies a quintessential application of digital twin technology. Significant advancements in its foundational technologies have the potential to enhance production flexibility, dynamic adaptability, and responsiveness in discrete production processes. This report centers on the exploration and deployment of digital twin systems tailored for discrete manufacturing. It elucidates the pivotal role of digital twin technology within the manufacturing milieu, detailing the comprehensive interconnectivity of the workshop’s elements—human, machine, material, method, and environment. Furthermore, it discusses the establishment of a central data computation hub, the validation of multi-dimensional applications on the virtual platform, and the development of sophisticated digital twin software utilizing the UE4 engine.
2.
Tianjie Fu
Zhejiang University
Title: Digital twin-driven smelting process management method for converter steelmaking
Abstract
The converter is an indispensable key equipment in the steelmaking industry. With the increasing demand for high-quality steel, the requirements for monitoring and controlling the status of the converter during the smelting process are also increasing. Personnel have difficulty fully understanding, analyzing, and managing the smelting process, resulting in low production efficiency and inability to achieve sustained high-quality results. A management method for converter steelmaking process based on digital twin technology is proposed to address the issues of low level of virtual visualization and insufficient monitoring capabilities.
3.
WenXiaojian
Donghua University
Title: MetaTwin: Enhancing Digital Twin with Fine-Grained Decomposition and Cross-Scale Assembly
Digital twin technology has emerged as a powerful paradigm in the field of manufacturing, enabling virtual representations of physical assets and processes. However, the current state-of-the-art digital twin systems often face challenges in effectively capturing and representing complex systems with diverse scales and levels of granularity. To address these limitations, this paper proposes MetaTwin, a novel approach that enhances digital twin capabilities through fine-grained decomposition and cross-scale assembly. MetaTwin introduces a hierarchical structure that allows for the decomposition of a digital twin into smaller, more manageable components, each representing a specific aspect or subsystem of the physical system. This fine-grained decomposition enables greater flexibility in modeling and simulation, allowing for the representation of complex systems at different levels of detail. Additionally, MetaTwin incorporates a cross-scale assembly mechanism that facilitates the seamless integration of these decomposed components, enabling the creation of digital twins that span multiple scales and levels of granularity.